ASES OFFERS EXPERT QA/QC SERVICES, PROVIDING EFFECTIVE PLANNING, SITE INSPECTION, AND MONITORING TO ENSURE YOUR COMPLETED BUILDING MEETS THE EXPECTED QUALITY STANDARDS
Quality in construction is paramount, aligning the final product with the needs of owners and users. Whether you’re an owner, architect, contractor, or manager, quality is the key focus. In the realm of Quality Management, both Quality Assurance (QA) and Quality Control (QC) are essential. ASES offers QA and QC services for government and commercial projects across the U.S., Canada, and Mexico. From plan reviews to site inspections, we collaborate closely with clients to ensure cost-efficient and precise fulfillment of their needs
Construction Quality Advisory and Monitoring Services
The objective of having a construction quality assurance plan is to ensure that the project is completed on time, within budget, and to the required quality standards. Third-party quality audit services provide an independent assessment of a project’s progress and quality.
The common cause of poor quality is the absence of an effective quality control plan for construction works. Quality inspection engineers often lack the independence and freedom that their role deserves. Quality checks are either bypassed, or defects and non-conformities are brushed under the carpet. To overcome this, more and more clients are now choosing to use “Third Party Quality Control” (TPQC) services
List of our construction QA QC services
- One time or Periodic Quality Audits
- Advisory to improve Construction Quality
- Organization wide improvement through implementing QMS
- Third party Quality Control
- Digitise Quality Control with the best in class QUALMANN App
- Any combination of the above
Construction Quality with the 3-Phase Inspection Model by USACE
In the realm of construction projects, ensuring quality, efficiency, and compliance with regulations is paramount. To achieve this, the United States Army Corps of Engineers (USACE) has implemented a robust inspection methodology known as the 3-phase inspection model. This model encompasses three critical phases, each tailored to specific aspects of construction, guaranteeing that projects meet required standards and mitigate potential issues. In this article, we will explore the key elements of the 3-phase inspection model and how it fosters first-time quality and successful project outcomes.
Phase 1 – Preparatory Phase: Setting the Foundation for Success
The Preparatory Phase is the crucial initial step in the 3-phase inspection model. Its primary objective is to lay the groundwork for seamless construction execution while mitigating costly problems that could arise during the project lifecycle. During this phase, a preconstruction meeting is conducted, bringing together stakeholders, including the owner, contractors, and subcontractors. Several key elements are discussed and addressed, including:
Scheduling and Long Lead Items: Ensuring that the project timeline is clearly defined, and potential delays are minimized by identifying long-lead items early on. Government/Authority Approvals: Addressing any necessary permits, clearances, or approvals required before commencing construction to avoid regulatory issues. Key Personnel: Identifying and appointing key personnel responsible for specific aspects of the project, establishing clear lines of responsibility.
The desired outcomes of the Preparatory Phase are as follows:
Agreement on Construction Process and Requirements: Ensuring that all parties involved are on the same page regarding the construction process and project specifications. Risk Assessment and Mitigation: Identifying potential project risks and formulating actionable plans to minimize or mitigate their impact. Inspection Plan and Checklists: Creating a comprehensive inspection plan that includes required inspections and hold points, backed by checklists incorporating critical verifications. Work Readiness: Verifying that all necessary elements are in place, giving the green light to begin construction safely and efficiently.
Phase 2 – Initial Phase: Ensuring a Strong Start
The Initial Phase takes place in coordination with the project’s Quality Control Plan for each Definable Feature of Work (DFOW). As work commences, this phase serves as a vital checkpoint to guarantee that the process aligns with established standards and expectations. Key activities during this phase include:
Reviewing Preparatory Phase Meeting Notes: Ensuring that the decisions and plans established in the Preparatory Phase are carried forward. Verifying Preparedness: Ensuring that all necessary preparations have been taken, such as procurement of materials and equipment. Understanding Quality and Safety Risks: Ensuring that all involved parties are fully aware of the risks pertaining to both quality and safety, and measures to address them are implemented. Acceptability of Initial Work: Supervising the initial stages of work, closely monitoring the process, and allowing progression only when satisfied with the quality of work.
Phase 3 – Follow Up Phase: Maintaining Quality to the Finish Line
The Follow Up Phase serves as a continuous monitoring process, ensuring quality is upheld from project initiation to completion. Throughout this phase, comprehensive inspections are conducted, and any deficiencies are noted and promptly addressed. The key components of the Follow Up Phase include:
Monitoring Work Progress: Using pictures, videos, daily reports, and detailed documentation to keep track of all aspects of contractor performance. Conducting Inspections: Regularly inspecting the ongoing work to ensure compliance with established standards. Reporting and Corrective Action: Noting any identified deficiencies and promptly reporting them to the relevant parties. Subsequently, verifying that the necessary corrective actions are taken to rectify the issues.
The 3-phase inspection model employed by the United States Army Corps of Engineers (USACE) is a comprehensive and structured approach to construction project management. By meticulously covering the Preparatory Phase, Initial Phase, and Follow Up Phase, the model ensures that each project adheres to established quality standards, prevents costly problems, and fosters collaboration between all stakeholders. As a result, the 3-phase inspection model plays a pivotal role in facilitating successful construction projects that meet their objectives efficiently and with a commitment to excellence.
We Make Quality our Priority
Our Third-Party Quality Control and Quality Assurance services are designed to be client-friendly, offering affordable costs and delivering the highest standards. We prioritize meeting our clients’ expectations by providing flexible resource deployment and customizable solutions. With a reputation built on satisfying customer requirements, we bring extensive experience across all sectors.
Avoid costly mistakes by conducting timely quality audits. As a construction professional, you understand the importance of quality assurance in project success. We assess the quality control of contractors and the Project Management team at intervals agreed upon by the Client.
A robust “Project Quality Plan” is established through audits tailored to our client’s needs and project requirements. ASES has developed an app for complete paperless data capture and analysis. Our engineers conduct audits, whether one-time or periodic, and record the findings in a completely paperless process
Key Aspects Addressed in Quality Assurance
Quality assurance (QA) involves various aspects:
- Qualification: Ensuring that your employees possess the necessary qualifications and skills required for the project.
- Materials: Verifying that construction materials meet the correct size, shape, standard, and material specifications for the job.
- Project management: Establishing clear expectations, timelines, budgets, and restrictions, and ensuring fair bidding procedures are in place.
- Equipment: Assessing whether the equipment is adequate and appropriate for the project’s scope.
- Rules governing quality: Implementing clear guidelines outlining what constitutes good quality and ensuring adherence to these standards
Making the Most of Construction Quality Assurance Observations
Construction projects can benefit from Quality Assurance (QA) observations in many ways. Examples of quality assurance in construction include:
- Defining quality: At the onset of construction, quality must be clearly defined, documented, and communicated to all stakeholders.
- Reviewing plans: Comprehensive review and assessment of plans and designs should occur at the start to prevent conflicts during construction.
- Considering materials: Equipment and materials must meet your standards, and verification of quality is essential.
- Centralized communication: Stakeholders should be informed, and project status should be shared regularly.
- Final observations: Once construction is complete, QA must also be involved during snagging and handover processes
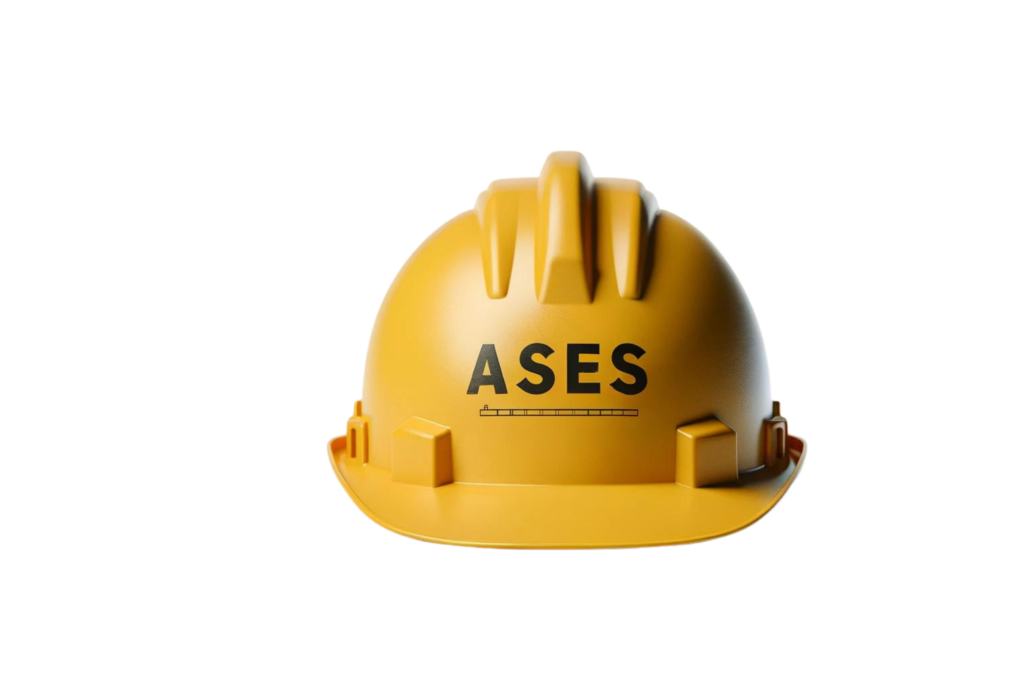
We Deliver On Our Quality Promise
Reliable construction services are hard to find. When you trust ASES, you are rewarded with a partner dedicated to building a long-term relationship. Submit your information to start building on your ideas.